齒輪在我們?nèi)粘I钪幸蕾嚨脑S多產(chǎn)品的性能中起著至關(guān)重要的作用。當(dāng)我們想到齒輪時(shí),我們通常將它們分為兩類(lèi):運(yùn)動(dòng)承載和動(dòng)力傳輸。承載運(yùn)動(dòng)的齒輪通常是有色金屬或塑料,而承載動(dòng)力傳輸齒輪通常由鐵合金制成。這里的重點(diǎn)是熱處理用于重型服務(wù)的齒輪。
要了解熱處理為何重要,請(qǐng)考慮材料科學(xué)模型。產(chǎn)品性能能力的最終用途是由其機(jī)械、物理和冶金性能定義的,這些性能由通過(guò)特定熱處理工藝生產(chǎn)的零件微觀結(jié)構(gòu)決定。
齒輪制造的感應(yīng)加熱處理工藝選型及分析
預(yù)硬化工藝
在齒輪制造過(guò)程中通常會(huì)進(jìn)行幾次熱處理,以便為預(yù)期的制造步驟準(zhǔn)備零件。這些對(duì)于制造優(yōu)質(zhì)齒輪至關(guān)重要。
退火
退火包括加熱并保持在合適的溫度,然后以合適的速率冷卻,主要是為了軟化零件并提高其可加工性。超臨界或完全退火涉及將零件加熱至高于臨界溫度 (AC3) — 即冷卻過(guò)程中奧氏體開(kāi)始轉(zhuǎn)變?yōu)殍F素體的溫度,然后在爐中緩慢冷卻至 600ºF 左右。臨界間退火涉及將零件加熱到高于最終轉(zhuǎn)變溫度 (AC1) 的溫度,這是加熱過(guò)程中奧氏體開(kāi)始形成的溫度。亞臨界退火將零件加熱到剛好低于 AC1 點(diǎn),然后在爐中緩慢冷卻。隨著退火溫度接近 AC1 部分,軟化速率迅速增加。
正火
正火包括將零件加熱到高于臨界溫度,然后在爐外進(jìn)行空氣冷卻,以消除齒輪毛坯中的殘余應(yīng)力,并確保尺寸穩(wěn)定性。通常從熱和微觀結(jié)構(gòu)的角度考慮正火。在熱學(xué)意義上,正火是奧氏體化,然后在靜止或輕微攪拌的空氣或氮?dú)庵欣鋮s。在微觀結(jié)構(gòu)的意義上,歸一化會(huì)產(chǎn)生更均勻的結(jié)構(gòu)。歸一化部件非常易于加工,但比退火部件更硬。正火在控制滲碳過(guò)程中的尺寸變化方面也起著重要作用。
壓力緩解
應(yīng)力消除涉及加熱到低于較低轉(zhuǎn)變溫度的溫度,如在回火中,保持足夠長(zhǎng)的時(shí)間以減少殘余應(yīng)力并足夠緩慢地冷卻(通常在空氣中),以盡量減少新殘余應(yīng)力的發(fā)展。應(yīng)力消除熱處理用于消除由于制造步驟而鎖定在齒輪中的內(nèi)部應(yīng)力。
硬化工藝
各種熱處理工藝旨在提高齒輪硬度。這些通常涉及加熱和冷卻,通常分為通過(guò)硬化、表面硬化(滲碳、碳氮共滲、滲氮、氮碳共滲)和通過(guò)施加能量(火焰、激光、感應(yīng))硬化。
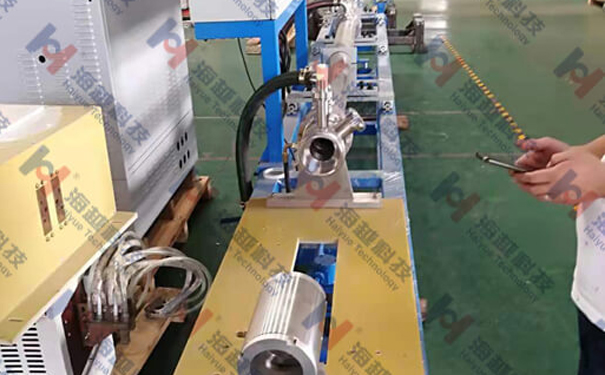
完全或直接硬化是指不產(chǎn)生外殼的熱處理方法。常見(jiàn)的淬硬齒輪鋼的例子是 AISI 1045、4130、4140、4145、4340 和 8640。重要的是要注意,不應(yīng)假設(shè)整個(gè)齒輪齒的硬度均勻。由于齒輪的外部比內(nèi)部冷卻得更快,因此會(huì)形成硬度梯度。最終硬度取決于鋼中的碳含量;硬度的深度取決于鋼的淬透性以及淬火強(qiáng)度。
可以在齒輪齒被切削之前或之后進(jìn)行徹底硬化。在零件硬化后切割齒輪齒時(shí),表面硬度和機(jī)械加工性成為重要因素,特別是考慮到機(jī)械加工會(huì)將部分或大部分硬度較高的材料去除到奧氏體范圍內(nèi),通常為 815 至 875°C( 1500 至 1600°F),然后進(jìn)行淬火和回火。
表面硬化
表面硬化在延展性、抗震性內(nèi)部或核心的頂部產(chǎn)生堅(jiān)硬、耐磨的外殼或表面層。表面硬化背后的想法是將輪齒的核心保持在 30 到 40 HRC 左右的水平以避免齒斷裂,同時(shí)硬化外表面以增加抗點(diǎn)蝕性。表面硬度值越高,抗點(diǎn)蝕性越大。當(dāng)表面硬度達(dá)到約 50 HRC 時(shí),彎曲強(qiáng)度增加,之后彎曲強(qiáng)度的增加被缺口敏感性的增加所抵消。
滲碳
滲碳是最常見(jiàn)的表面硬化方法。一個(gè)適當(dāng)滲碳的齒輪將能夠比淬火齒輪多處理 30-50% 的負(fù)載。滲碳鋼通常是含約 0.10% 至 0.20% 碳的合金鋼。常用滲碳鋼的例子包括 AISI 10148、4320、5120、8620 和 9310 以及國(guó)際牌號(hào),例如 20MnCr5、16MnCr5、ZF-7B、20MoCr4 和 V2525。
滲碳可以在 1475-2000°F (800-1090°C) 的溫度范圍內(nèi)進(jìn)行。今天的行業(yè)慣例發(fā)現(xiàn)大部分滲碳操作發(fā)生在 1600-1850°F(870 至 1010°C)。滲碳層深度可以在 0.005 到 0.25 英寸(0.13 到 8.25 毫米)的范圍內(nèi)變化。然而,對(duì)于低于 0.015 英寸(0.4 毫米)的表面深度,通常使用碳氮共滲工藝。
碳氮共滲
碳氮共滲是滲碳工藝的改進(jìn),而不是滲氮的一種形式。這種改進(jìn)包括將氨引入滲碳?xì)夥罩校员阍跐B碳外殼生產(chǎn)過(guò)程中向滲碳外殼中添加氮?dú)?。通常碳氮共滲的齒輪鋼的例子包括 AISI 1018、1117 和 12L14。
通常,碳氮共滲在比滲碳更低的溫度下完成,或者在 1330-1650°F (700-900°C) 之間,并且時(shí)間更短。由于氮會(huì)抑制碳的擴(kuò)散,因此通常會(huì)導(dǎo)致比滲碳零件的典型情況更淺的情況。碳氮共滲外殼的深度通常在 0.003-0.030 英寸(0.075-0.75 毫米)之間。
氮化
滲氮是另一種增加表面硬度的表面處理工藝。由于不需要快速淬火,尺寸變化保持在最低限度,這是一個(gè)主要優(yōu)點(diǎn)。并非適用于所有齒輪材料。其局限性之一是產(chǎn)生了極高的表面硬度或“白層”,比滲碳產(chǎn)生的表面更脆。盡管如此,氮化已被證明是許多應(yīng)用的可行替代方案。通常的氮化齒輪鋼包括 AISI 4140、4150、4340、7140、8640 和 AMS 6475(Nitralloy N)。
氮化通常在 925-1050°F (495-565°C) 范圍內(nèi)進(jìn)行。對(duì)于生產(chǎn)優(yōu)質(zhì)且一致的氮化物外殼和可預(yù)測(cè)的尺寸變化而言,三個(gè)極其關(guān)鍵的因素是鋼成分、先前結(jié)構(gòu)和核心硬度。表面深度和表面硬度特性不僅隨滲氮的持續(xù)時(shí)間和類(lèi)型而變化,而且還受這些因素的影響。通常,外殼深度在 0.008-0.025 英寸(0.20-0.65 毫米)之間,需要 10 到 80 小時(shí)才能生產(chǎn)。
氮碳共滲
氮碳共滲是滲氮的一種改進(jìn)形式,而不是滲碳的一種形式。在這里,當(dāng)鋼處于鐵素體狀態(tài)時(shí),即在低于加熱過(guò)程中奧氏體開(kāi)始形成的溫度下,氮和碳同時(shí)被引入鋼中。在此過(guò)程中會(huì)形成非常薄的“白色”或復(fù)合層,以及下面的擴(kuò)散區(qū)。與滲氮一樣,不需要快速淬火。通常進(jìn)行氮碳共滲的齒輪鋼的例子包括 AISI 1018、1141、12L14、4140、4150、5160、8620 和某些工具鋼。
氮碳共滲通常在 1025-1110°F (550-600°C) 下進(jìn)行,可用于產(chǎn)生等效的 58 HRC 最低硬度,該值隨基材而增加。白層深度范圍為 0.00005-0.0022 英寸(0.0013 至 0.056 毫米),典型的擴(kuò)散區(qū)域?yàn)?0.0013-0.032 英寸(0.03-0.80 毫米)。
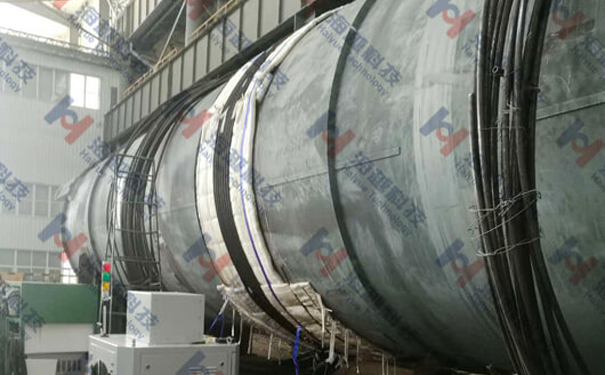
在齒輪的制造中使用了各種通過(guò)施加能量進(jìn)行淬火的方法,包括火焰淬火、激光表面淬火和感應(yīng)淬火。
火焰硬化
通過(guò)旋轉(zhuǎn)或漸進(jìn)式加熱技術(shù),火焰硬化可用于小型和大型齒輪。在漸進(jìn)式加熱方法中,火焰逐漸加熱火焰頭前面的齒輪。有時(shí)必須通過(guò)逐漸增加行駛速度或通過(guò)預(yù)冷來(lái)補(bǔ)償這種影響。通過(guò)這種技術(shù)可以硬化多種齒輪材料,包括普通碳鋼、滲碳等級(jí)、鑄鐵和某些不銹鋼等級(jí)。
主要的操作變量是火焰頭或叉的移動(dòng)速度;火焰速度和氧燃料比;內(nèi)火焰錐體或燃?xì)馊紵鞯焦ぷ髋_(tái)面的距離;以及淬火的類(lèi)型、體積和角度。許多小批量火焰硬化操作的成功取決于操作員的技能。
激光表面硬化
激光表面硬化用于提高齒輪等高應(yīng)力機(jī)械零件的機(jī)械性能和表面硬度。由于大型工業(yè)激光器的成本較高,而且 0.16-0.20 英寸的材料帶無(wú)需多次重疊即可硬化,因此用于表面處理的激光器的使用相對(duì)有限。從能量的角度來(lái)看,激光不是很有效,增加了費(fèi)用。AISI 1045、4340 和鑄鐵(灰色、可鍛和延展性)等齒輪材料是該技術(shù)的理想選擇。
感應(yīng)淬火
感應(yīng)淬火通常用于齒輪的熱處理。該過(guò)程使用交流電來(lái)加熱齒輪齒的表面。然后對(duì)該區(qū)域進(jìn)行淬火,導(dǎo)致加熱區(qū)域的硬度增加。它通常在相對(duì)較短的時(shí)間內(nèi)完成。鋼的類(lèi)型、其先前的微觀結(jié)構(gòu)和所需的齒輪性能特征決定了所需的硬度分布以及由此產(chǎn)生的齒輪強(qiáng)度和殘余應(yīng)力分布。外部正齒輪和斜齒輪、錐齒輪和蝸輪、齒條和鏈輪通常采用感應(yīng)淬火。典型的齒輪鋼包括 AISI 1050、1060、4140、4150、4350 和 5150,感應(yīng)淬火后盡快消除應(yīng)力或回火可降低開(kāi)裂風(fēng)險(xiǎn)。
感應(yīng)加熱產(chǎn)生的硬度圖案取決于所用感應(yīng)器的類(lèi)型和形狀以及加熱模式。一種用于齒輪感應(yīng)淬火的技術(shù)是使用線圈環(huán)繞零件。在實(shí)踐中,這個(gè)圓周感應(yīng)器從尖端向下硬化牙齒。雖然這種模式對(duì)于花鍵和一些齒輪裝置是可以接受的,但在點(diǎn)蝕、剝落、齒疲勞和耐久性等問(wèn)題的較重負(fù)載齒輪需要更像滲碳情況下的硬度模式。這種類(lèi)型的感應(yīng)淬火稱為輪廓淬火,是通過(guò)應(yīng)用單次或掃描模式通過(guò)逐齒或逐間隙技術(shù)產(chǎn)生的。圖案均勻性對(duì)線圈定位非常敏感。
與輪廓硬化具有相同效果的另一種方法是使用雙頻。使用 3 或 10 kHz 的預(yù)熱使核心溫度上升到略低于奧氏體化溫度。然后根據(jù)齒輪的要求,單元變?yōu)橹蓄l或高頻。這種方法的優(yōu)點(diǎn)是更短的循環(huán)時(shí)間。在非常大的齒輪中,輪廓加熱將更具成本效益,因?yàn)榫€圈隨著尺寸的增加而變得非常昂貴。
后硬化工藝
硬化后,齒輪通常要經(jīng)過(guò)幾個(gè)熱處理和機(jī)械加工步驟。
回火
下臨界溫度(AC1)以下的任何溫度均可用于回火,但最終回火溫度是使用中所需的硬度、強(qiáng)度和韌性的平衡。在 300-400°F (150-200°C) 范圍內(nèi)回火對(duì)于齒輪來(lái)說(shuō)是常見(jiàn)的,它會(huì)稍微增加韌性,這對(duì)于大多數(shù)需要高強(qiáng)度和抗疲勞性的應(yīng)用來(lái)說(shuō)是足夠的,其中負(fù)載主要是壓縮。有時(shí)對(duì)齒輪進(jìn)行雙重回火以確?;鼗鸱磻?yīng)的完成并促進(jìn)所得微觀結(jié)構(gòu)的穩(wěn)定性。
零下處理
目前使用兩種類(lèi)型的低溫處理:-120°F (-85°C) 的“淺”冷卻和 -300°F (-185°C) 的“深”冷卻。在某些情況下,這種處理與隨后的回火操作相結(jié)合。
深冷處理的目的是轉(zhuǎn)化殘余奧氏體,提高淬火態(tài)組織的硬度。此外,通常還可以獲得更好的尺寸穩(wěn)定性。亞零處理的最終目標(biāo)是提高耐磨性、改善彎曲疲勞壽命和最小化殘余應(yīng)力。如今,低溫處理在高性能齒輪中很常見(jiàn)。
噴丸強(qiáng)化
噴丸強(qiáng)化是一種冷加工過(guò)程,其中齒輪表面用稱為丸粒的小球形介質(zhì)進(jìn)行轟擊。噴丸強(qiáng)化是一個(gè)受控過(guò)程,在該過(guò)程中,介質(zhì)的尺寸、形狀和速度受到仔細(xì)監(jiān)測(cè)和控制。齒輪噴丸處理的一個(gè)常見(jiàn)要求是對(duì)齒根進(jìn)行噴丸處理,齒面允許有過(guò)噴。噴丸處理不應(yīng)與噴丸處理(一種清潔工藝)混淆。
噴丸會(huì)在齒輪表面產(chǎn)生殘余壓應(yīng)力,從而增強(qiáng)齒的彎曲疲勞性能。殘余壓應(yīng)力抵消了可能導(dǎo)致彎曲材料失效的施加拉應(yīng)力。
材料選擇
動(dòng)力傳動(dòng)齒輪使用多種鋼和鑄鐵。在所有齒輪中,必須在仔細(xì)考慮最終用途所需的性能和總制造成本后,才能選擇材料,并考慮加工經(jīng)濟(jì)性等問(wèn)題。關(guān)鍵的設(shè)計(jì)考慮需要分析施加的載荷類(lèi)型,無(wú)論是漸進(jìn)的還是瞬時(shí)的,以及所需的機(jī)械性能,例如彎曲疲勞強(qiáng)度或耐磨性,所有這些都定義了核心強(qiáng)度和熱處理要求。
齒輪齒廓的不同區(qū)域有不同的服務(wù)需求。必須考慮作用在輪齒上的力,其中輪齒彎曲和接觸應(yīng)力、抗劃傷和耐磨性以及疲勞問(wèn)題是最重要的。例如,在根部區(qū)域,需要良好的表面硬度和高殘余壓應(yīng)力以提高耐久性或彎曲疲勞壽命。在中徑處,必須結(jié)合高硬度和足夠的表面強(qiáng)度來(lái)處理接觸應(yīng)力和磨損并防止剝落。
影響疲勞強(qiáng)度的因素很多,包括:
硬度分布,作為表面硬化、表面深度、核心硬度的函數(shù)
顯微組織,作為殘余奧氏體百分比、晶粒尺寸、碳化物(尺寸、類(lèi)型、分布)、非馬氏體相的函數(shù)。
缺陷控制,作為殘余壓應(yīng)力、表面光潔度、幾何形狀、晶間韌性的函數(shù)
在整個(gè)制造方案中,材料選擇過(guò)程、工程設(shè)計(jì)和制造之間必須存在協(xié)同關(guān)系。為了優(yōu)化齒輪設(shè)計(jì)的最終性能,必須在每個(gè)學(xué)科的優(yōu)先級(jí)之間取得平衡。這通常不是一件容易的事。
盡管材料僅占制造典型齒輪成本的一小部分(約 10%),但材料選擇必須是原材料成本和性能能力的完美結(jié)合。了解材料中存在的每種合金元素的功能及其對(duì)合金物理性能的影響對(duì)于材料選擇至關(guān)重要。通過(guò)材料選擇來(lái)平衡的特性包括拉伸強(qiáng)度、屈服強(qiáng)度和沖擊強(qiáng)度,以及伸長(zhǎng)率。
對(duì)于許多齒輪應(yīng)用,需要 30 到 40 HRC 范圍內(nèi)的核心硬度,即齒輪齒的橫截面中心。為了達(dá)到這種硬度,在選擇材料時(shí)需要考慮零件截面尺寸和齒輪節(jié)距尺寸。如果芯部硬度太低,在高負(fù)荷下將無(wú)法支撐外殼;如果太高,可能會(huì)在殼/芯接口處發(fā)生齒輪齒的“碎裂”。
以上是關(guān)于齒輪制造的感應(yīng)加熱處理工藝選型及分析。更多關(guān)于感應(yīng)加熱處理的相關(guān)技術(shù)知識(shí),請(qǐng)咨詢青島海越機(jī)電--中頻高頻電磁感應(yīng)加熱設(shè)備制造商。