早在今天的許多技術(shù)進(jìn)步之前,人們就已經(jīng)對(duì)金屬進(jìn)行了熱處理,以改善特定應(yīng)用的物理和化學(xué)性能。在中世紀(jì),鐵匠鍛造和回火金屬(盡管以相對(duì)粗糙的方式)來(lái)制造刀片、工具和日常生活用品?,F(xiàn)在,冶金學(xué)家和材料工程師擁有更廣泛的專業(yè)技術(shù)和設(shè)備,可以根據(jù)特定應(yīng)用定制材料。但是有許多不同的感應(yīng)加熱處理,例如淬火、回火、時(shí)效、應(yīng)力消除和表面硬化。
為了消除混淆,下面是最常見(jiàn)的感應(yīng)加熱處理,以及它們的目的和優(yōu)缺點(diǎn)。
退火
退火涉及升高金屬的溫度,直到它處于由其相圖定義的平衡狀態(tài)。它用于改變金屬的物理特性,例如硬度,但也可能發(fā)生局部化學(xué)變化,具體取決于相變。退火處理通常在機(jī)械加工之后進(jìn)行,例如機(jī)加工和磨削,甚至其他熱處理,例如淬火。
淬火和回火
淬火涉及將鋼加熱到其臨界溫度以上并在那里保持足夠長(zhǎng)的時(shí)間,以使微觀結(jié)構(gòu)完全轉(zhuǎn)變?yōu)閵W氏體相。然后對(duì)鋼進(jìn)行淬火,該過(guò)程通過(guò)將鋼放入水、油或聚合物溶液中來(lái)快速冷卻鋼。這“凍結(jié)”了它的微觀結(jié)構(gòu)。鋼的淬火冷卻控制了冷卻速度,冷卻速度決定了淬火后的微觀結(jié)構(gòu)。冶金學(xué)家使用金屬的時(shí)間-溫度-轉(zhuǎn)變圖(TTT 圖)來(lái)預(yù)測(cè)由此產(chǎn)生的微觀結(jié)構(gòu),無(wú)論是馬氏體、貝氏體還是珠光體。通過(guò)這些結(jié)構(gòu),碳成分大于 0.3wt% 的鐵合金??赡芊浅?jiān)硬 (>60 HRC),尤其是馬氏體結(jié)構(gòu)。但是硬度的增加伴隨著韌性的降低。
回火,一個(gè)退火過(guò)程,淬火后。鋼在淬火后變得非常硬和脆,因此它經(jīng)歷了另一個(gè)步驟以降低其硬度并增加其延展性,同時(shí)保持其微觀結(jié)構(gòu)。
在臨界溫度以下回火鋼可以使其保持馬氏體結(jié)構(gòu),但如果回火時(shí)間足夠長(zhǎng),它會(huì)轉(zhuǎn)化為鐵素體和小碳化物的混合物,其確切尺寸取決于回火溫度。這使鋼更柔軟,更具延展性。關(guān)鍵的回火參數(shù)是溫度和時(shí)間,必須精確控制它們以產(chǎn)生所需的最終硬度。較低的溫度在消除內(nèi)應(yīng)力的同時(shí)保持較高的硬度,而較高的溫度會(huì)降低硬度。
在初始鑄造或機(jī)械加工后,淬火和回火賦予鋼以制造具有材料特性的零件的硬度和強(qiáng)度。然后可以將零件加工成最終狀態(tài)。淬火和回火會(huì)使金屬變形,因此零件在最終加工之前總是要經(jīng)過(guò)這兩個(gè)過(guò)程。對(duì)于具有用于修改表面特性的附加熱處理工藝的零件,淬火和回火決定了零件的核心特性,例如硬度、強(qiáng)度和延展性。(其他表面硬化處理將在后面介紹。)
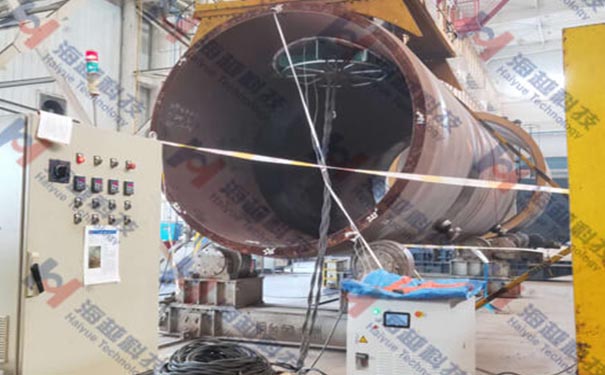
應(yīng)力消除,即退火步驟,在研磨、冷加工、焊接或最終加工之后,在金屬淬火和回火至所需的微觀結(jié)構(gòu)和強(qiáng)度后進(jìn)行。這意味著必須特別考慮以確保工件的退火溫度不會(huì)太接近其回火溫度。這可以防止改變先前獲得的硬度和微觀結(jié)構(gòu)。
應(yīng)力消除可去除內(nèi)部位錯(cuò)或缺陷,使金屬在最終加工(如氣體或離子滲氮)后尺寸更加穩(wěn)定。應(yīng)力消除不是為了顯著改變金屬的物理特性;事實(shí)上,硬度和強(qiáng)度的變化是不需要的。
沉淀硬化
沉淀硬化是一種特殊的退火步驟,也稱為時(shí)效硬化,因?yàn)槟承┙饘贂?huì)在亞臨界溫度下隨時(shí)間硬化。如上所述,這種強(qiáng)化金屬的方法僅限于那些經(jīng)過(guò)淬火處理并且是過(guò)飽和溶液的金屬,這意味著材料相對(duì)于存在的相而言處于非平衡狀態(tài)。
在這些合金中,過(guò)飽和馬氏體溶液被加熱(500°至 550°C)并保持 1 至 4 小時(shí),讓沉淀均勻地成核和生長(zhǎng)。這導(dǎo)致非變形、高拉伸和屈服強(qiáng)度鋼具有比未時(shí)效狀態(tài)更好的耐磨性能。析出相、成分和尺寸取決于時(shí)效合金,但都具有相同的強(qiáng)化材料的一般效果。
并非所有鐵合金都符合這種硬化機(jī)制,但馬氏體不銹鋼(如 17-4、15-5 和 13-8)以及馬氏體時(shí)效鋼都是很好的候選材料。(“馬氏體時(shí)效”一詞結(jié)合了“馬氏體”和“時(shí)效”這兩個(gè)詞。這些鋼具有優(yōu)異的強(qiáng)度和韌性而不失去延展性,但不能保持良好的切削刃。時(shí)效是指延長(zhǎng)的熱處理過(guò)程。)對(duì)于這些合金,過(guò)飽和馬氏體溶液被加熱(500°至 550°C)并保持 1 至 4 小時(shí),讓沉淀均勻地成核和生長(zhǎng)。這導(dǎo)致非變形、高拉伸和屈服強(qiáng)度鋼具有比未時(shí)效狀態(tài)更好的耐磨性能。
感應(yīng)淬火
感應(yīng)淬火很像淬火,但有一個(gè)明顯區(qū)別:感應(yīng)淬火中的加熱是有選擇性的。這是因?yàn)樵诟袘?yīng)淬火中,加熱是通過(guò)設(shè)計(jì)用于匹配零件幾何形狀的磁性線圈進(jìn)行的。這意味著可以強(qiáng)化關(guān)鍵零件特征,而不會(huì)強(qiáng)化零件的核心。相反,核心保留了金屬的強(qiáng)度和延展性。就像傳統(tǒng)的淬火一樣,它是使用水、油或聚合物溶液完成的。
可以在碳含量大于 0.3wt% 的鋼上進(jìn)行感應(yīng)淬火,并且可以對(duì)具有專為它們?cè)O(shè)計(jì)的感應(yīng)線圈的尺寸和幾何形狀的零件進(jìn)行感應(yīng)淬火。感應(yīng)淬火還顯著減少了淬火零件所需的加工時(shí)間,并降低了脫碳的風(fēng)險(xiǎn)。與傳統(tǒng)的加熱和淬火不同,感應(yīng)是一種表面受限的熱處理,硬化深度范圍為 0.5 至 10 毫米。
表面硬化
表面硬化熱處理,包括滲氮、氮碳共滲、滲碳和碳氮共滲,會(huì)改變零件的化學(xué)成分——與前面提到的退火技術(shù)不同——并專注于其表面特性。根據(jù)加工時(shí)間和溫度,這些工藝會(huì)產(chǎn)生深度為 0.01 到 0.25 英寸的硬化表面層。由于額外的加工時(shí)間,使硬化層更厚會(huì)導(dǎo)致更高的成本,但零件的延長(zhǎng)磨損壽命可以很快證明額外的加工成本是合理的。材料專家可以應(yīng)用這些工藝為特定應(yīng)用提供最具成本效益的零件。
滲碳和碳氮共滲
滲碳非常適用于需要在表面進(jìn)行額外硬化以提高耐磨性但需要更軟的核心以獲得卓越強(qiáng)度的零件。滲碳是一種高溫工藝(900 至 950°C),涉及碳向鋼中的添加和擴(kuò)散。這些溫度高于鋼的臨界溫度,因此隨后的淬火讓富含碳的表面形成馬氏體,而核心保持較軟的鐵素體和/或珠光體結(jié)構(gòu)。硬化深度可以厚達(dá) 0.25 英寸,具體取決于零件在滲碳溫度下浸泡的時(shí)間。
如前所述,滲碳的優(yōu)點(diǎn)是具有高硬度的深層耐磨層。這是齒輪、刀片和切割工具的理想選擇。滲碳用低成本合金鋼和低碳鋼(例如 1008、1018 和 8620)制造堅(jiān)硬耐用的零件。原始合金可能導(dǎo)致完全硬化或塊狀馬氏體結(jié)構(gòu)。還應(yīng)注意,滲碳溫度會(huì)導(dǎo)致某些零件變形。
對(duì)于不含大量促進(jìn)硬化的合金元素的低碳鋼,在工藝中添加氮可以提高表面硬度。添加氮稱為碳氮共滲。碳氮共滲通常在比滲碳 (850°C) 稍低的溫度下進(jìn)行,因此變形較小,但它也減少了硬化深度(對(duì)于可比的處理時(shí)間)。碳氮共滲過(guò)程中產(chǎn)生的硬化表面雖然更薄,但確實(shí)具有更高的硬度和更高的加工溫度(如回火和應(yīng)力消除)。
滲氮和氮碳共滲
高溫滲碳/碳氮共滲的替代方法是滲氮/氮碳共滲. 它還產(chǎn)生硬化的表面層和類似的耐磨性,但它會(huì)將氮擴(kuò)散到整個(gè)表面層(不是碳),并且它使用亞臨界加工溫度。滲氮的典型溫度范圍為 450° 至 575°C。這意味著零件可以在其最終加工狀態(tài)下進(jìn)行加工,幾乎沒(méi)有變形,因此幾乎不需要氮化后加工(如果有的話)。較低的溫度還可以保持所需的核心微觀結(jié)構(gòu)和物理特性,同時(shí)針對(duì)給定應(yīng)用修改表面層。選擇滲氮時(shí)要考慮的一個(gè)注意事項(xiàng):將任何應(yīng)力消除、時(shí)效或回火溫度告知熱處理人員,以防止改變核心特性。
與僅限于低碳含量鋼的滲碳不同,通過(guò)滲氮可以為多種合金提供 600 至 1,200 Hv 的表面硬度。但最適合滲氮的合金通常含有標(biāo)稱量的微合金元素:Cr、V、Ti、Al 和 Mo。滲氮對(duì)于含有大量鉻 (10+wt%) 的不銹鋼和工具鋼極為有益。這些氮化鋼的表面硬度可遠(yuǎn)高于 70 HRC,非常適合長(zhǎng)期耐磨。
滲氮也不限于這些類型的鐵合金,因?yàn)榈吞间撘部梢杂不?。除了產(chǎn)生硬化、耐磨的表面外,滲氮還會(huì)形成復(fù)合區(qū)。復(fù)合區(qū)是滲氮過(guò)程中在表面形成的富氮層,堅(jiān)硬、耐磨(>60 HRC 當(dāng)量)和耐腐蝕。這有利于低碳和低合金鋼,如果不存在復(fù)合區(qū),這些鋼將不會(huì)被考慮用于惡劣的環(huán)境條件。
滲氮/氮碳共滲合金的硬化深度通常在 0.005 到 0.030 英寸之間,具體取決于工藝的時(shí)間和溫度。更深的硬化層需要更多的時(shí)間。復(fù)合區(qū)厚度可達(dá) 0.002 英寸。厚,這是哪種合金是氮化物、時(shí)間和溫度的函數(shù)。零件如何滲氮也會(huì)影響區(qū)域深度。氮化可以通過(guò)氣體或離子(等離子體)進(jìn)行。
氣體滲氮使用裂解氨作為氮源,在正壓環(huán)境中進(jìn)行。它是大批量批量加工的理想選擇,并且在溫度均勻性和具有深孔或通道的滲氮零件方面也非常出色。不建議對(duì)多孔零件進(jìn)行氣體滲氮,因?yàn)闅怏w流過(guò)孔會(huì)導(dǎo)致嚴(yán)重的脆化。離子滲氮非常適合選擇性滲氮,因?yàn)榱慵梢詮牡入x子體中屏蔽以防止?jié)B氮。
離子滲氮是通過(guò)在真空中在陽(yáng)極和零件(陰極)之間施加電位差來(lái)進(jìn)行的。這種電位差形成氮等離子體(一種獨(dú)特的紫色光),迫使氮原子進(jìn)入零件的暴露表面。
等離子滲氮非常適合合金,例如不銹鋼,因?yàn)樗梢钥焖俜纸忖g化氧化物表面。通常,由于等離子體的持續(xù)濺射,離子氮化鋼比氣體氮化鋼具有更薄的化合物區(qū)域。但這對(duì)于某些應(yīng)用來(lái)說(shuō)可能是理想的,例如齒輪,在這些應(yīng)用中,接觸應(yīng)力可能會(huì)損害具有過(guò)多復(fù)合區(qū)域的表面。
在比較氮化和氮碳共滲時(shí),后者通常在更高的溫度 (575°C) 下進(jìn)行,并使用碳源。碳的加入形成了更硬、更耐磨、潤(rùn)滑度更高的層。更厚的復(fù)合區(qū)也可以通過(guò)氮碳共滲形成。相比之下,純氮滲氮環(huán)境會(huì)形成堅(jiān)硬耐磨的層,但不如氮碳共滲。那么為什么不總是引入使用氮碳共滲呢?引入碳會(huì)增加表面孔隙率,這對(duì)接觸應(yīng)力大的零件不利。所得層的延展性也較差。
材料選擇還決定了哪種加工技術(shù)最適合應(yīng)用。
本通用指南解釋了一系列熱處理。但工程師在考慮熱處理時(shí)牢記以下有關(guān)其零件設(shè)計(jì)的問(wèn)題很重要:我的零件受到什么力?他們?cè)谑裁喘h(huán)境下工作?應(yīng)用是否需要表面、核心或特定表面區(qū)域的不同屬性?
更多關(guān)于感應(yīng)加熱處理的方案,請(qǐng)咨詢青島海越機(jī)電--中頻高頻電磁感應(yīng)加熱設(shè)備制造商。